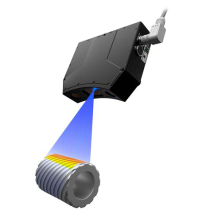
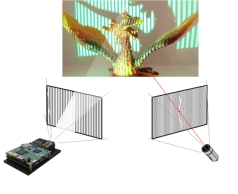
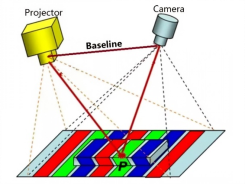
3D machine vision is an optical imaging technique that quickly and accurately captures the physical details of an object's surface. With digital 3D scan data, the dimensions of any object (including surface area, volume, and feature dimensions) can be extracted.
Structured light is a typical 3D imaging principle in 3D machine vision, which projects a series of encoded raster patterns onto an object, receives the distortion information of these patterns through a camera or sensor, and then uses image processing and triangulation algorithms to convert these distortion data into 3D point clouds. The point cloud can be used directly to analyze object surface dimension information or easily exported to a variety of CAD modeling formats.
DLP technology is a portable programmable structured light solution with high resolution and high accuracy in 3D structured light technology. 3D imaging systems based on DLP technology can generate highly accurate, non-contact 3D data in real-time for 3D machine vision scanning/measurement purposes.
Features and benefits of DLP Programmable Structured Light:
– Fast, programmable graphics rates up to 32 kHz
– Acquire 3D scan data of moving objects in real time.
– Optimize scanning speed and accuracy across multiple objects and environments with adaptive graphics sets.
– Precise depth capture
– Achieve sub-μm measurement accuracy.
– Digital switches using reliable reflective MEMS micromirrors
– Virtually unaffected by color and environment, maintaining performance over time and temperature.
– Active illumination via LED, laser, or bulb
– Multiple wavelengths to scan a wide range of materials.
– Achieve excellent low-light performance.
Example Applications:
– Factory automation
– Industrial robots
– Medical imaging
– Dental Scan/Intraoral Scan (IOS)
– Industrial metrology
– Biometrics